Tungsten Carbide Rod Powder Extrusion Molding Key Technologies
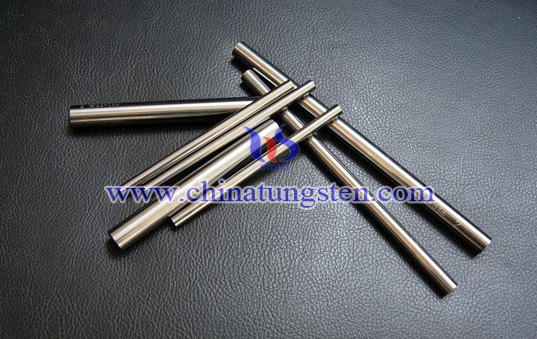
The following is the extrusion manufacturing process of tungsten carbide rod powder extrusion molding, the material properties of tungsten carbide rods are related to links, such as original powder, binder, mixing, extrusion, degreasing, sintering and so on.
Basic manufacturing process of powder extrusion molding
1、Powder
Existing WC-Co powder milling technology is not the limiting extruded rod of the main factors used in tungsten carbide. Swedish company Sandvik gas reduction and carbonization technology, the Japanese company Sumitomo Electric and Tokyo tungsten carbide direct reduction in rotary kilns (1350 ~ 1650 ℃) technology, the U.S. company OMG rapid carbothermal reduction (1500 ~ 2000 ℃) technology (from Dow Chemical Company purchase) production Asian micro / nano WC powder; U.S. Nanodyn company spray - thermal conversion technology to produce WC-Co composite powder (purchased from Rutgers University). Engaged in Asian micro / nano WC powder developed units more, but for WC-Co composite powder developed by small units.
2、Binder
Binder system with tungsten carbide rod powder extrusion molding process development constantly updated, and increasingly complex. Properly designed system, the molding process must meet the requirements of the powder fluidity under the premise of full consideration of the extruded bars degreasing process performance, the selection and formulation forming agent and removal of forming agent and the final product performance together. Early binder system based mainly in paraffin, and currently to a multi-component direction. Groups such as foreign element forming agent LDPE (low density polyethylene) / SA (stearic acid) and PP (polypropylene) / SA (stearic acid), the domestic three-component molding agent 20/SBS (styrene - butadiene - styrene block polymer) +75 / PW (paraffin) +5 / SA (stearic acid), etc.
3、Mixing
Kneading to improve the powder flowability and the completion of the dispersing a complex process, in this step, the preforming agent must be completely and uniformly coated with the powder, mixed into a powder having excellent rheological properties of material. Inadequate mixing, mixing time, temperature, methods, leading to improper control of the important reasons bad shape. Only through the mixing process to get the best rheological properties of the powder, it may be forming an internal crack, smooth surface of the rod body green.
4、Extrusion
Extruded rod is the key to mold design. Although there has been able to shape diameters from 0.5mm to 40mm rod, but also in improving the accuracy achieved important progress, but most of the mold design is still the rule of thumb, CAD system is difficult to be well applied to tungsten carbide powder crowded rod compression molding process. With extrusion rheology theory research and experience, mold design and production time will be greatly reduced and it will be more use of multi-cavity extrusion die to improve efficiency. Meanwhile, with the development of technology will make the pre-pressure, squeezing pressure, extrusion speed, extrusion temperature, etc., affect the quality of good or bad rod establish contact a number of factors to determine the best technology program.
5、Skimmed
Degreasing to guarantee the quality of the rod is very important. Generally, the binder forming billet volume accounted for 40% of a 60% by weight of 6% to 10%, in the process of forming billets skim prone to macro and micro defects. Heating rate, holding time and temperature, atmosphere, forming formulations, are the important factors of the process. Commonly used methods of thermal degreasing degreasing, solvent degreasing, catalytic skimmed, skimmed and siphon supercritical fluid extraction. Different methods have their advantages and disadvantages defatted, simply adopt a comprehensive manner forming agent is difficult to remove, the specific selection of the degreasing method, according to the different molding formulations, combined with a variety of skim ways.
6、Sintering
Sintered carbide powder extrusion molding rod last a link, it plays a densification of the product and chemical properties of a uniform role performance and accuracy of the product has a very important influence. Since the tungsten carbide powder extrusion molding rod used in a large binder, the sintering shrinkage is very large (generally linear shrinkage of 12% to 18%), so that there is a distortion control and dimension control problems, plus tungsten carbide powder extruded rod is shaped pieces, this problem becomes more prominent.
In particular, the sintering temperature, atmosphere and heating rate control, carbon accuracy and performance of the product a great impact. Currently, the rod by means of vacuum sintering sintering + HIP (hot isostatic pressing) and low pressure sintering. Plasma discharge sintering (SPS), microwave sintering and some fast, low temperature, the advantages of uniform sintering technology has become a new hotspot....
»» PDF Extended reading:
Tungsten Carbide Rod Forming Technology
New Process Study Tungsten Carbide Rod Cutting