Tungsten Carbide Rod Powder Extrusion Molding Development Status
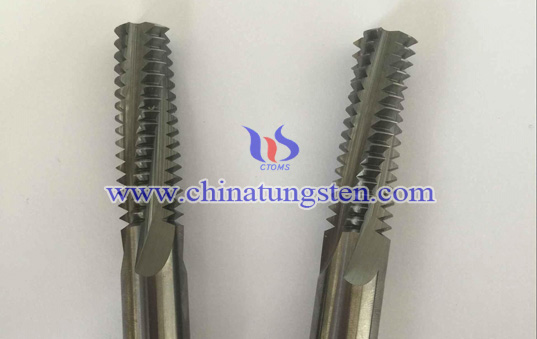
since 1980s, there has been a wide use of continuous extruding equipment represented by twin-screw vacuum extruder in powdered plastics extrusion. The automation and accuracy has been greatly improved, and they use a lot of optoelectronic monitoring and computer online-control and so on, thus further facilitate the operation and improve the molding capabilities.
With the emergence of modern extruding equipment and continuous development, the powder extrusion technology is improved, and mow rods with diameters of 0.5~40mm can be produced. Products contain the PCB micro drills, electronic printing pins and other industrial precision components, automotive joint bar and other powder metallurgy products, as well as components in traditional fields.
The U.S. ATM company extruded micro twist drills out of WC-Co mixture for printing circuit board. And the German Konrad Friedrichs corporate created various carbide rods with helical coolant holes, the maximum diameter can reach 38mm; mass percent of drill is 6~15 and the minimum grain size is 0.5μm. German G-Elit plant had extruded rods long as 2100mm.
Dr. Friedrichs from German made a statistics towards the production growth of tungsten carbide rods used in drills, end mills, reamers, and so on. In 1998, the world's total production has reached 6500t, among with 4900t were not perforated, and 1600t were with parallel or helical coolant holes, which is about 5~7% of high-speed steel rods of global annual demand. During the 12~15 months within 1999 and 2000, the tungsten carbide rods' production has been doubled and reach to 13000t, which replaced high speed steel to a great degree and occupied an increasingly important status.
»» PDF Extended reading:
Tungsten Carbide Rod Forming Technology
New Process Study Tungsten Carbide Rod Cutting