Tungsten Carbide Rod Cold Isostatic Molding Process
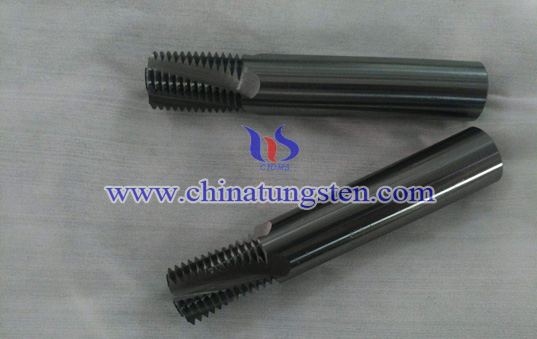
Tungsten carbide rod forming the traditional process can be divided into Cold isostatic press-ing(CIP), and molding and other processes. Although rarely used, but in certain situations it also is essential.
1、Pressure Cutting Method
The sieved after grinding carbide powder is pressed into a block, and by cold isostatic pressing treatment, and then subsequent processing. In this process, as long as a small amount of plasticizer, such as paraffin, polyethylene and ethanol. If cold isostatic pressure is high enough (400 MPa), and even not add a binder. Rods which made out of this method have rather rough surface, and before finished, they must be grinded and turning processed.
2、Wet bag method
The mould is averagely under the same high pressure liquid(about 200MPa), the specimen size is limited by the cavity, thus it's not suitable for mass production. This method is mainly for diameter bar(Figure 1).
3、Dry bag method
In this measurement, different fluids are used as pressure medium, and the mould is semi-stationary. The adding and removing of the blanks are operated under dry condition. There are high degree of automation and shorter operation cycle, which make it suitable for bulk molding(Figure 2). By this means, the length of finished rods are longer than those of mechanical molding method(with the longest up to 400mm), with a small amount of wax or polyvinyl alcohol(1% to 1.5%).
In addition, the use of dry-bag method can produce a rod with cooling channels. The outer surface of the blank machined spiral groove, the spiral groove into elastic fibers into the mold to the body, the body blank and the mold with a powder filling the gap between, and pressure for dry bags phantoms in of the blank and the particles are pressed together, the tank intense deformation elastic fibers. In subsequent dewaxing and sintering, the forming agent from the powder, evaporated on rough and elastic fibers, so that the cooling channels are produced with a rod. As manufacturing method, and the rough soft, manufactured by the positional accuracy of the cooling channels is not high.
»» PDF Extended reading: tungsten carbide rod forming technology